Products

Power Distribution Unit (PDU)
-
Design Authority
-
Electrical Power Management
-
Modular control/management of aircraft electrical power
-
Integrates to a CSC or can be a stand alone unit
-
AC and DC power control and distribution
-
No buss bars, all power handled via high current PCBA
-
All functionality contained within a single enclosure
-
All circuit breakers centralized within the PDU

VFR HeliSAS Autopilot & Stability Augmentation
- Design Authority
​​
This rugged, yet lightweight, Flight Control Computer (FCC) was designed to meet our customers demanding requirements and represents our most sophisticated product. These requirements included light weight, low cost, robustness against helicopter levels of shock and vibration, and ability to operate through challenging EMI environments that are commonly encountered near busy airports.

IFR HeliSAS Autopilot & Stability Augmentation
- Design Authority​
​
This Flight Control Computer (FCC) was designed as a part of the Genesys HeliSAS Stability Augmentation and Autopilot System for light and medium helicopters. Genesys has STC’s for several helicopter models by the major suppliers. Due to the full two channel redundancy, this FCC is certified for Instrument Flight Rules (IFR) use. This Stability Augmentation / Autopilot is self-contained with all of the electronic components necessary for full functionality. Typical external inputs include Pitot Tube altitude, airspeed, and a GPS solution.

F O Engineering EETRS
(Extreme Environment
Thermal Regulation System)
- Design Authority
​
F O Engineering designed, integrated, and delivered key components for the M-ATV portable radar cooling system. The components included the Cooling System Controller, Compressor Motor Driver, and a 26V to 300V (3000W) Power Converter. These components were designed and tested for the harsh environments of ground-based vehicles. The System Controller communicated via an ethernet interface to the vehicle's management system.
The System Controller then monitored the many pressure and temperature sensors within the system and adjusted the compressor operating point to optimize cooling efficiency under a wide range of environments. The Power Converter took the available 26V from the vehicle and created the high-voltage power source required by the Compressor Motor Driver.

F O Engineering DSC
(KC-46A Hydraulic Hose Reel
Drive System Controller)
-
Design Authority
-
F O Engineering is a primary contributor to Centerline
-
Drogue Refueling System Integration
All hardware and firmware developed by F O Engineering -
Flight Qualified equipment to MIL-STD-810 and RTCA DO-160G requirements
-
DO-178B Level B software development
-
The DSC contains all refueling system control laws
-
The DSC communicates via ARINC 429​

P-8 Poseidon Fuselage Fuel Dump Valve
-
Design Authority
-
Dual redundant architecture
-
6 units per flight vehicle
-
Currently 12 P-8 Poseidons are flying
-
Full digital servo loop
-
Automatic calibration at assembly
-
Onboard EMI filter

A-160 Hummingbird Control Systems
-
Design Authority
-
Main and Tail Rotor Actuator Controls
-
Landing Gear and Utility Actuator Controls
-
No Skid Brake Actuator Control
-
Cooling Fan Controls (Avionics and Engine)
-
Complete actuator integration
-
Multiple transducer types
-
Up to 50 Hz bandwidth requirement
-
Common Software for all applications
-
9 HP in a 7 cu. in. controller​

Falcon 900
-
Design Authority​
-
Inhibits 2nd speed brakes above 320 knots
-
Protects against wing overloading associated with the addition of a winglet kit
-
DO-160F Qualified to combination of external and internal environments
-
DO-178B, level C Software was accomplished by F O Engineering
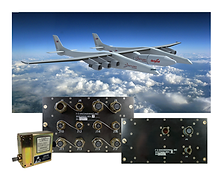
Stratolaunch Actuation Subsystems
-
Design Authority
-
Subsystems included:
o Nose and Main landing gear steering
o Landing gear extension and retraction
o Pilot and co-pilot electric braking
-
Hardware included:
o Comand Distribution Unit (CDU)
o Common Actuation Module (CAM)
o Rotary Electromechanical Actuator
-
F O Engineering designed all hardware and firmware.
-
F O Engineering is the primary subsystem integrator
-
DO-178 Level C certified software.